What Types of Alloy Matter When Choosing a Rod or Wire to Weld Stainless Steel?
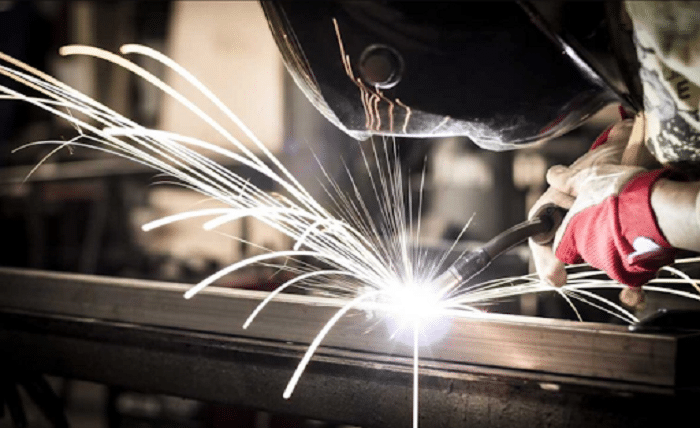
Welding rod or wire choice plays an important role in type and quality of finish of your work. Now before we get into the actual welding of stainless steel, it is important to realize that all alloys are not created equally and as a result, much of the process specific consumables and techniques defined in this post may be difficult – yet rewarding— starters for you at any level.
Note: Discover the best stainless steel welding wire with us! As an authorized dealer of all major brands used by professionals, we offer the largest stock of welding supplies. Visit our website at https://www.udo.co.th/product/detail/yawata-316l-16 to explore our products or seek expert welding advice from our specialists. Don’t miss out on the highest quality and availability in the market!
Regardless of how experienced you are at welding stainless steel, understanding the alloy types and how they behave while being forged is integral to your success whether you have seasoned experience or you are a novice.
A Guide to Welding Stainless Steel
Stainless steel which is very corrosion resistant with high tensile strength and aesthetic appearance made it widely used material, particularly in the construction, automotive as well as food processing industries. However, these same properties also create some problems when welding. Stainless Stainless is also not a very good conductor of heat and it tends to expand about 8 times more than most metals when heated. That will lead to deformities or cracks if you make a mistake with the welding.
To prevent these issues, it is important to select an appropriate welding rod or wire which corresponds with the alloy type of stainless steel being welded. This guarantees compatibility and efficient functionality with fewer defects.
The Importance of Alloy Types
Stainless steels can be divided into three primary families depending on the alloy: austenitic, ferritic and martensitic. All four types have their own characteristics when it comes to weldability.
300 series (austenitic stainless steel)
Type 304: This is the most used stainless steel having good corrosion resistance with very good ductility. All lies down under it are mainly 304 and 316. The suggested rod or wire for welds for austenitic stainless steel is YAWATA 316L-16. These are made for machining high chromium and nickel foundry dirt, so you get a nice, clean weld that has strength.
430 (Approx) Ferritic Stainless Steel: 400 Series
Ferritic stainless steel will not form austenite and is therefore less ductile but corrosion resistant, magnetic. This kind of stainless metal is regularly found in automotive parts and commercial equipment. The rods or wires that are used must be of similar composition — special care has to be taken to ensure they will not crack and the weld won.
Martensitic Stainless Steel
Though still stainless, martensitic types are not as corrosion resistant as austenitic or ferritic types, but they are hard and strong. It has a very high carbon content, and so requires preheating before welding and specific rods or wires.
Selecting that Perfect Welding Rod or Wire
When choosing a welding rod or wire, the following factors have to be taken into consideration:
Base Metal Composition
The filler metal or wire must always be the same alloy as or compatible with the base stainless steel. However, if consumables are not selected correctly, weak welds or corrosion problems can occur.
Operating Environment
Rod or wire selection is primarily decided by the environment in which the welded stainless steel will be used. For example, using a rod like YAWATA 316L-16 provides exceptional saltwater resistance in the most corrosive environments, like those found during marine applications.
Welding Process
Different rods/wires are used for each welding process, such as TIG, MIG and stick welding. However, while TIG welding of stainless steel is still often considered the best method due to its precision, for larger Got Parts projects it makes more sense to use MIG and stick.
Certifications and Quality Assurance
Make sure that welding consumables you are using always have a reputation and proper tests conducted. These high quality steps using YAWATA 316L-16 stainless steel welding wire are really to be trusted for industrial journeys as they fulfill international quality rubrics.
Avoiding Common Stainless Steel Welding Pitfalls: Here Are Some Helpful Tips
Less Heat: The greater heat is overheated that will distort or change the strength of stainless steel. Only run a gentle heat, and also let the factor cool down each passing.
Avoid Cross Contamination: Use different sets of tools and cleaning agents to minimize contact with other metals. Stainless steel’s corrosion resistance is a surprisingly delicate property that can be lost by even a small amount of contamination.
Use Shielding Gas: If you are working with a process like TIG or MIG welding, always use the correct shielding gas (argon is often a good choice) to avoid oxidation and maintain a clean weld environment.
YAWATA 316L-16S Perfect for Stainless Steel Welding
For those who require a quality welding rod that can be used for stainless steel projects consistently, you cannot go wrong with YAWATA 316L-16, which continues to outperform all in its class. This rod is optimal for austenitic stainless steel, which has great corrosion resistance in chloride-laden areas. With a low carbon content, it reduces the chances of carbide precipitation and durable welds free from defects.
It is highly versatile, which allows this rod to be used in a variety of chemical tanks and piping systems as well as architectural structures. Visit UDO Welding Wire to learn more about the YAWATA 316L-16 and discover the ideal solution for your stainless steel welding project.
Conclusion
Stainless steel welding is only as successful as the choice of welding rod or wire suited to the alloy type and project. Welding various stainless steel alloys can be used in many places, but different consumables should also be selected according to their characteristics and alloy types; YAWATA 316L-16 sounds a suggestion for choosing high-quality manufacturing consumables. When you prepare for a complex industrial project or simple household repair, the correct equipment and knowledge will help!
Visit UDO Welding Wire for additional information and a range of quality stainless steel welding products, and step up your welding game today!